Fire protection for Luxury Spa.
Fire Protection for Luxury Spa
Customer requirements
Nirvana Spa is a leading luxury relaxation and leisure venue in the South of the UK.
Spanning a large site with multiple interconnected areas it contains five separate pool areas, numerous treatment rooms, saunas, gyms, changing rooms as well as restaurants, kitchen facilities and staff areas.
RES was brought in to manage, improve and service the fire alarm system and other fire protection equipment.
Extending the site
The spa has quadrupled in size over the few past years with additional wings being added phase by phase to accommodate new pool areas, treatment rooms and changing facilities.
RES have continuously expanded the original fire alarm system to accommodate the new phases.
Additional fire alarm system “loops” have been added over time to ensure every space is adequately protected with additional call points and detectors.
Ensuring zero disruption
Key to the success of the Spa is ensuring a tranquil and holiday-like environment at all times of the day.
RES works closely with the spa to co-ordinate that the maintenance and servicing is carried out “out of hours” with zero disruption
to its customers.
Furthermore, our engineers are trained to leave each site immaculately clean and tidy.
Delivering customer satisfaction
The spa now contains over a hundred fire protection appliances such as extinguishers and fire blankets and over six hundred fire alarm devices such as manual call points, control panels and detectors – all carefully managed and serviced throughout the year by RES.
RES continues to provide Nirvana Spa with reliable and responsive fire protection services to meet their needs.
“Nirvana Spa are delighted with the high level of professional service R.E.S. provide and the fire protection we now have throughout our facilities which gives us a great deal of reassurance”
Neil, Maintenance Director, Nirvana Spa
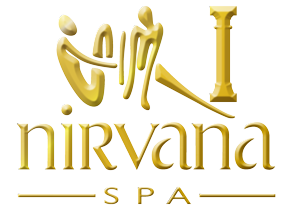